Summary:
The mechanical properties of stainless steel forgings can be improved through heat treatment and su...
The mechanical properties of
stainless steel forgings can be improved through heat treatment and surface treatment, so that they can meet the requirements of use conditions. Different use environments also put forward clear requirements for the treatment of the steel grades of stainless steel forgings. Stainless steel forgings must also have certain mechanical properties, which is the basis for realizing the use value of stainless steel forgings. Today we will learn about several commonly used methods for processing stainless steel forgings. It is precisely because of different processing methods that different shapes of stainless steel forgings can be formed.
1. Milling
The milling cutter rotates as the main motion, and the stainless steel forgings and the milling cutter do the cutting processing method for the feed motion. Milling is one of the main processing methods of plane. During milling, the rotation of the stainless steel forging with the milling cutter of the worktable is the main movement.
2. Broaching
A method of processing the inner and outer surfaces of stainless steel forgings by using a broach to move axially under the action of pulling force. Using a multi-tooth broach, a very thin metal layer is cut from the workpiece one by one, so that the surface can reach a higher precision, and a smaller roughness value can be obtained for stainless steel forgings.
3. Drilling
The drilling tool and the stainless steel forgings move relative to each other and make an axial feed movement. The method used by the forging factory to process holes on the stainless steel forgings. Drilling is the most basic hole processing method in the processing of stainless steel forgings.
4. Turning
The stainless steel forging is rotated as the main movement, and the turning tool is the cutting method for the feed movement. The main movement of turning processing in the forging plant is the rotating movement of stainless steel forgings, which is especially suitable for processing stainless steel forgings of wheels and shafts of rotating surfaces. The linear movement of the tool is the feed movement.
5. Grinding
The grinding tool rotates at a higher linear speed, and the forging factory processes the surface of stainless steel forgings. Usually the use of abrasive tools for processing is called a grinder. In the grinding process, the self-sharpening effect of the grinding wheel is the cutting edge of the general tool that other cutting tools do not have.
6. Boring processing
The main movement is the rotation of the boring tool, which is a cutting processing method for stainless steel forgings or the feed movement of the boring tool. Boring processing is mainly carried out on milling and boring machines. Boring is the further processing of the drilling of stainless steel forgings. Boring can enlarge the hole diameter, improve the accuracy, reduce the surface roughness, and can better correct the deviation of the original hole axis. Boring can be divided into rough boring, semi-fine boring and fine boring.
7. Planing
The cutting processing method in which the planer and the stainless steel forging are reciprocated in a relatively straight line in the horizontal direction. Planing is one of the main methods of plane processing, and it is the most commonly used processing method for plane processing of single-piece small batch production of stainless steel forgings. Common planer machine tools include bullhead planer, double planer and slotting machine.
For the above several commonly used processing methods, forging plants will use different processing methods according to the different shapes required to produce stainless steel forgings. There are also many other methods of processing stainless steel forgings. Although the processing principles of these methods are different, they still have a lot in common. The biggest difference is that the cutting motion forms are different when processing stainless steel forgings. However, because of the different machine tools and tools used, they have their own technological characteristics. And the scope of application.
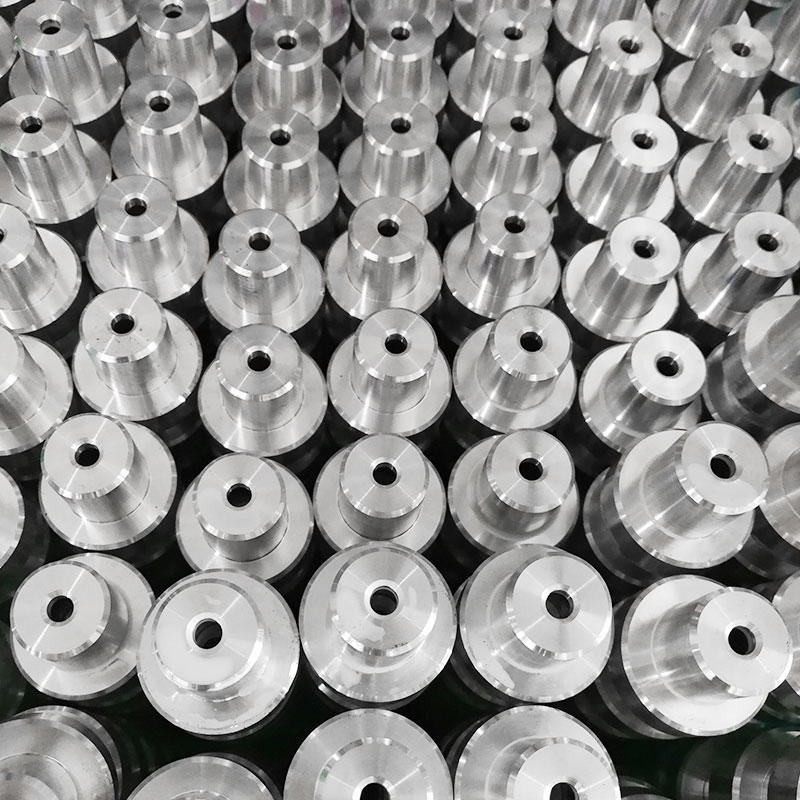