Summary:Before starting the machine, a comprehensive and detailed inspection of the CNC machine parts should...
Before starting the machine, a comprehensive and detailed inspection of the
CNC machine parts should be carried out, including the operation panel, guide rail surface, jaws, tailstock, tool rest, tools, etc., which can be used only after confirmation.
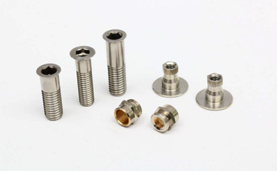
1. After the CNC lathe parts are powered on, check whether the switches, buttons and keys are normal and flexible, and whether the machine tool is abnormal.
2. After the CNC lathe part program is input, the CNC lathe processing code, address, numerical value, sign and decimal point should be carefully checked.
3. Correctly measure and calculate the workpiece coordinate system. And check the results obtained?? · Input the workpiece coordinate system, and adjust the coordinates. Coordinate values, positive and negative signs, and decimal points are carefully checked
4. Before the workpiece is installed, run the program once to see if the program can be carried out smoothly, whether the installation of tools and fixtures is reasonable, and whether there is "overtravel".
5. When cutting, the quick override switch needs to be turned to the lowest gear.
6. When the CNC lathe part is cutting and feeding, when the tool runs to the workpiece 30 ~ 50mm, it is necessary to verify whether the remaining values of the Z-axis and X-axis coordinates are the same as the processing program under the feed hold.
7. During the cutting and processing of CNC lathe parts, after sharpening the tool and replacing the tool, the tool position should be re-measured and the tool compensation value and tool compensation number should be modified.
8. After the CNC lathe part sequence is modified, carefully check the modified part.
9. The machine tool can only be started after the workpiece is clamped. It is forbidden to measure and touch the workpiece when the workpiece is rotated.
10. When there are abnormal phenomena such as workpiece jumping, shaking, abnormal sound, loosening of fixtures, etc., it needs to be stopped.
11. After the emergency stop, the machine tool should be used again to "return to zero" before the program can be run again.